About us We produce loudspeaker in accordance to our conviction ...
... that is why we develop and construct all monitors ourselves - from A to Z, from the electronics of the amplifier to the voice coil of the transducer. A product, which components all come from our own manufacturing, has noticeable advantages for you as a professional customer. We are independent of third parties products and build our components just the way we require them - this proceeding can't be beaten in quality by mass-production. This strategy also leads to high continuity and fixed values of our product range as well as it ensures that replacement parts will be available for long-term. We believe that this is the only way to create a product which is worth your investment and satisfies your professional needs for many years.
Our loudspeakers are ...
... the result of consequent development that needed many years and pursued only one aim: the highest degree of precise sound without any coloration regardless of genres. Hearing and measuring are the basis of our work. We build on profound musical comprehension and the knowledge of unalterable physical laws - not on magic tricks, new fashioned ideas or marketing-strategies.
... team players and no tonal „loners“. Which speaker is the optimum in an individual listening situation, is determined by listening distance, requested lower cut-off frequency and maximum sound pressure level – but not by tonal differences. A consistent application of our products enables an almost compatible sound/acoustic pattern, no matter if used in OB van or main control room, private listening room or concert hall. The on-site fabrication in our Saxon manufactury guarantees high class quality.
Technical solutions Tireless listening with our MCDS-Coax
The foundation of our speakers from the Studio-, high-end and partially the sound reinforcement is the application of our reliable and consequently improved coaxial technology (MCDS-Coax – Minimum Colouration Directivity Steering-Coax). The sound radiation from one point results in some important advantages: a homogeneous and colouration neutral sound pattern, sound localisation and sound staging without comparison. These features allow tireless listening.
A classic example is the human voice that is a sound source from on point for the listener. This relation is transferable to the individual sound sources in complex musical performances. When inline speakers are used/employed, where the low-, mid- and treble components are linearly arranged, the listener perceives the sound reproduction principally separated, because the sound events don't blend into one point. The separated hearing contradicts the human notion of a natural sound source and results in unnecessary stress by mental merging of the acoustic information into a consistent sound pattern and tonal perception. The technically optimal solution is therefore the consistently well-engineered MCDS-Coax from Musikelectronic Geithain.
Noncritical speaker placement through our K-technology
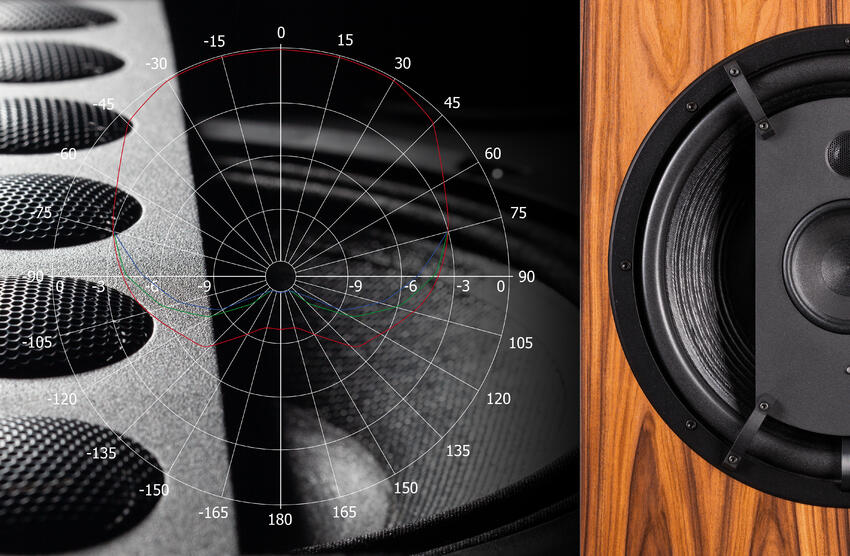
During sound reproduction in enclosed rooms reflections from the walls cause undesirable interferences in the bass range which are usually counteracted by purposeful speaker placement. This kind of optimisation depends on many factors and is rarely successful. With our K technology (“K” for the German translation of cardioid) we offer a solution that achieves outstanding results even in acoustically critical rooms. The specialists from Saxony achieve this with an acoustic propagation element with backward attenuation of more than 10 dB, which is integrated into the back of the cabinet. As a result the reflections behind the speaker are heavily attenuated so that interferences are barely recognisable.
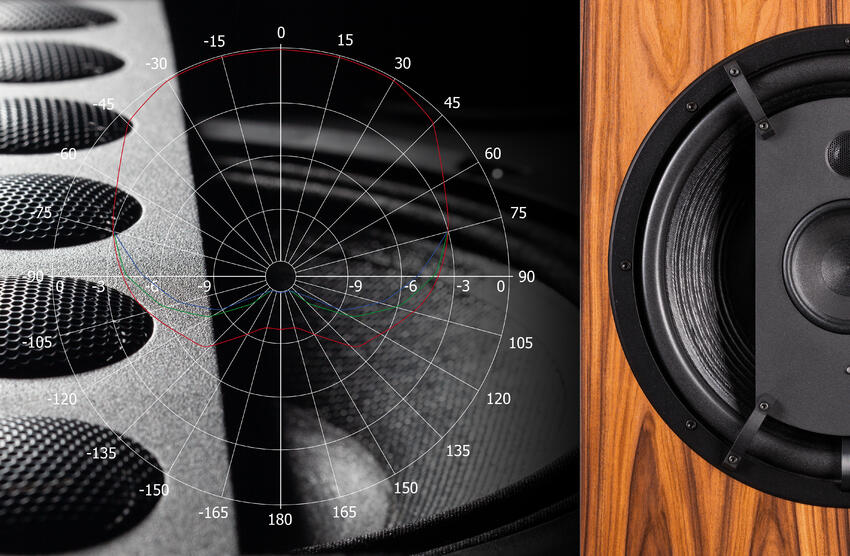
The perfect way for sound pressure level enhancement in the treble range
Often used sound transmission elements in front of tweeters enable a simple control of the directionality/directivity/directional characteristic but tend to unavoidable sound colouration. They originate from short term reflections on the inner surface of the horn. We use another path with our tweeter array and abandon systems with horn speakers to enhance the sound pressure level and bridging great listening distances. Coaxially arranged before the mid range system, the tweeter system guarantees the accustomed colouration neutral reproduction of music and speech and invokes the proximity to the sound event that is desired by the listener. This technology sets tonal and technical benchmarks in the studio, high-end and sound reinforcement segment.
The sum of all these constructive arrangements results in seamless tonal compatibility of our speakers to all other products from Musikelectronic Geithain. High sound colour neutrality, excellent spatiality and sound staging as well as tireless listening to most complex sound events distinguish all our speakers and are a unique at the speaker market.
History Company Foundation
On 5. Mai 1960, Joachim Kiesler, together with two watchmakers, founded the PGH "Fernsehen, Rundfunk, Uhren" (trade production cooperative "Television, Broadcast, Watches") in Geithain. A great success story began for the cooperative that was to grow from five employees (two of them being apprentices) to about 30 employees in 1972. During the first years the production cooperative was only active as service facility. In 1966 Joachim Kiesler started with first own development works.
In 1972 the cooperative was disappropriated and compulsorily nationalised. It became VEB (Volkseigener Betrieb – nationally-owned enterprise) Musikelectronic Geithain (MEG).
In 1992 a handful of former production cooperative members, headed by Joachim Kiesler, succeeded in retransferring the ownership of the VEB into private property. They founded the musikelectronic geithain gmbh (limited company), which is still successfully managed by Joachim Kiesler.
Products from back then
1966/67 saw the development of the TMV 1 transistor microphone amplifier, which was taken into in-house production in 1967.
In 1969 the TMV 2 transistor microphone amplifier was created, a further development of the TMV 1. Start of development and production of the SPR 6 six-channel mixing amplifier.
In 1970 the cooperative begins with the production of an in-house-developed power amplifier, which will go on the market known as LV 70. It finds its application in theatres, local cultural centres, cinemas etc.
In 1970, after one year of development work, the cooperative started producing the EO 1002 electronic concert and church organ, a two-manual instrument with pedal and 37 stops.
In 1972 a one-manual instrument of the same type was created, the EO 1001. With these developments, Joachim Kiesler aimed at an electronic emulation of the sound of pipe organs.
Music connoisseurs indeed attested the organs "the convincingly clear sound of good traditional organs". (Quote: Concertmaster Günther Siering, according to the Leipziger Volkszeitung newspaper from April 23, 1978. Similar opinions are known from the Leipzig director for church music Prof. Georg Trexler and from Hans Otto, organist to the Freiberg Cathedral.) The recognised high quality of this instrument revitalised the discussion about electronic emulation of pipe organs. A total of about 150 organs were built and installed in churches, civil registry offices, theatres, cultural centres (even in the Berlin Palace of the Republic) in the GDR, in Hungary and in Czechoslovakia, and they are partly still in use today. Each organ had been customised according to the respective location and was voiced on site.
In 1972 the V 910 and V 911 universal mixing power amplifiers were developed and produced.
1973/74 saw the development and production start of the V 733/34/35/36 studio power amplifiers.
In 1976 the development and production of the V 940 and V 941 power amplifiers and of the V 920 and V 921 mixing power amplifiers followed. Those were produced by MEG in large quantities until the political changes in the GDR.
In 1980 MEG develops the Uni 10 car loudspeaker for the Arnstadt Communication Equipment Factory. This loudspeaker was the first in the GDR to receive the coveted "Q" quality label. Until the political changes, about 9 million pieces were produced.
In 1980 development and production started of a wide range of sound reinforcement loudspeakers for cultural institutions, continuing until today.
In 1984, at the Leipzig Fall Trade Fair, MEG presented the prototype of the meanwhile legendary BR 25 loudspeaker. The West German "Funktechnik" (Radio me34_contentineering) magazine attested this development to have caught up with the international state-of-the-art.
The expected production quantity exceeded the personal capacity of MEG.. For this reason the development was sold to the VEB Statron Fürstenwalde in 1985. Until the political changes, about 650,000 units were produced, 50 % of which were exported to West Germany. This product, too, received the "Q" quality label, that by then had been granted only twice to loudspeakers, in both cases to MEG products. The BR 25 became one of the top-selling hi-fi loudspeakers in Germany.
In 1984 MEG developed the RL 900 broadcast studio control loudspeaker.
In 1985 mass production of the RL 900 started at MEG. The loudspeaker was installed in all broadcast and television institutions throughout the GDR. It also found application in several cultural institutions, for instance at the Leipzig Gewandhaus concert hall, the Dresden Semperoper opera house and the Berlin Schauspielhaus theatre.
In 1987 the BR 37 two-and-a-half-way loudspeaker and the BR 27 two-way loudspeaker were developed. Their production took place at Statron Fürstenwalde.
1987 also saw the start of production of the BR 50 3-way loudspeaker, another MEG development, at the Frankfurt/Oder Energie-Kombinat state combine. It also received the "Q" quality label.
In 1989/90 the German ARD network (Association of Public Broadcasting Corporations) staged a test for studio monitors. In this test, the RL 900 received the rating "best transparency and directional accuracy".
After the political changes in Germany, the RL product range conquered the international market. The monitors made by MEG found their way into the most renowned European broadcast and television studios, and also were popular as home loudspeakers to music freaks. Gerhard Steinke, one of the godfathers of German electro-acoustics, called the loudspeaker RL900 "a masterpiece of musical trade".
Awards and Honours
In 1992 the "Saxon Innovation Award for Economy" was granted to the musikelectronic geithain gmbh for the RL 900A and RL 904 studio monitors, which were developed by Joachim Kiesler.
In 2005 a meeting between the Saxon Minister for Economy, Thomas Jurk, and Joachim Kiesler took place in the acoustic reference room in our company.